PIPE EXTRUSION PROCESS
Pipes are produced by horizontal extruding molten polymer through an annular opening in to several sizing, cooling devices that stabilize the final dimensions. The elements of the production line are:
- Extruder
- Die
- Sizing device
- Cooling bath
- Puller
- Cutter
Materials:
The resin commonly used for the pipe manufactures are : PE, PVC, PS & ABS. For the pipe production the materials may have to be compounded. For example many pipe producers use PVC. The resin is heat sensitive and under the normal processing conditions, it has high viscosity, thus it can’t be processed-Its needs compounding. However appropriate grades of other polymers, such as PE or ABS, can be directly use as supplied by the manufacturer, without compounding.
PVC compounding is process in which additives are mixed with the base resin to get a homogeneous mixture. The additives are added to either improve process ability or enhance product performance. The following ingredients are added to PVC for pipe production:
- Plasticizer
- Heat Stabilizer
- Lubricants
- Fillers
- Processing aids
- Colorants
- Flame retardant
- Impact Modifier
- Plasticizers are used to make the resin softer, reduce the viscosity and thus make process of PVC easier. Epoxy and Di-ethyl hexyl phthalate (DOP) are example of common PVC plasticizers.
- Heat stabilizers are required to prevent the thermal degradation of PVC at the process temperatures. The degradation involves resin discoloration and evolution of HCL, In the process lead stabilizers have been used. Owing to toxicity of PB. Today the common stabilizers are based on tin viz. di-butyl tin maleate.
- Lubricants are used to reduce friction during processing that may lead to degradation. Two types of lubricants are used. External and internal. The former viz. calcium stereate and wax is used to reduce friction on process between metal surfaces to polymer. The latter stearic acid friction arising out of polymer chain for slippage.
- Fillers and reinforcement are added for cost reduction and improvement for mechanical properties of product. Both increase rigidity, hardness, density and flame retardancy. Typical filler is calcium carbonate, a typical reinforcement are chopped glass fiber and mica flakes, while such additives as clay, talc and silica are between.
- Flame retarding agents are needed for plasticized PVC. Chlorinated paraffin oil or waxes, oxide of Sb, Mo, P or B, as well as aluminum oxide have been used.
- Processing aids are added to rigid PVC to improve flow through the barrel and die. In to the group of additives belong polymer and co-polymers miscible with PVC ex. PMMA, ABS & SAN etc.
- Impact modifier are added to improve the impact strength impact modifier are at least two parts. One that ascertain miscibility with PVC and other elastomeric additives are used to make stiffing. Example MBS, CSR & NBR.
PVC compounding is usually carried out in two stages
- Dry blending PVC resin with additives in an intensive dry mixer, equipped with a high speed impeller.
- Melt blending in suitable compounder. E.g single screw extruder, twin screw extruder, multi screw extruder & kinetic energy mixer etc.
PVC pipe formulation:
Pipe Extrusion Line:
The pipe extrusion line comprises an extruder pipe die, sizing unit, cooling through, puller & cutter.
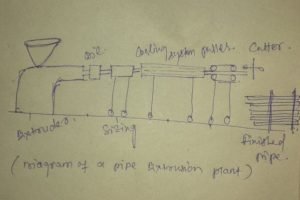
Pipe Extrusion Die:
The role of an extrusion die is to form the molten material delivered by the screw in to a required cross section. The extrusion die can be classified as straight: through cross head and offset dies, base on their attachment to the extruder.
Sizing Equipment:
The extruded emerging from the pipe die usually shows variation of diameter, caused by variable of the rhelogical melt property. Thus the pipe has to be calibrated or sized while hot.
Cooling water through:
- During the sizing also the pipe gets cooled.
- Cooling is done by spraying water over the surface of the pipe.
- This length of the cooling through PE is longer than for PVC.
Pulling Machines:
- Pulling machines maintain uniform pipe size
- Pullers are either the caterpillar type of the gripping wheel type.
- The puller speed is controlled by electrical electronic or magnetic speed vartiators.
Controls:
- They provide automatic measurement and control of pipe size
- In one system the capacitance of the pipe is measure and is related to the thickness
- The sensing head moves around the pipe, showing when the pipe is out of round and when it is generally too heavy or too light.
- All this systems can be made of feedback to control the puller or the extruder drive.
Cutting Device:
- Circular say cutters with blade special designed for cutter plastics are used to cut the plastic in to specified length.
- Automatic cutting device are also used. They travel with the pipe to cut than after cutting go back to pick up and the next pipe length.
- Larger size are sawed to length
Coiling Device:
- Smaller diameter PVC pipe are coiled on a large center wood reel.
- In simple methods pipe is coiled by a band rank.

Right
For LD and LLDPE material temperature
thanks for visiting the site..soon will upload that details
Hello Deepak,
We are looking for PVC and CPVC material composition for manufacture of pipes used for sanitary application. Request you to share the Composition for the same.
Regards,
Chandrashekhar, Bangalore
please tel me the right formula for produce PVC pipes we use PVC K 67 resign and we look for the right additive to produce good quality sewage pipes
Hi! Saurabh,
Could you please share your details so that I can reach you?
could u kindly make this article available in another format?
thanx