INJECTION MOLDING PROCESS FAULT & REMEDIES
Air traps (voids & bubbles):
An air trap is air that is cut inside the mold cavity. It becomes trapped by converging polymer melt fronts or because it failed to escape from the mold vents, mold insert, which also act as vents. Air trap locations are used in areas that fill last. Lock of vents of undersized vents in the last to fills areas are common of air trap and the resulting defects. Another common cause is race tracking (the tendency of polymer melt to flow preferantely in thicker section). Caused by a large thickness ratio.
Problems caused by air traps:
Entrapped air will result in voids and bubbles inside the molded part, sort shot incomplete fill or surface defects such as blemishes or burn marks. To eliminate air trap, you can modify the filling pattern by reducing the injection speed, enlarging venting, placing proper venting in the cavity.
Remedies:
Alter the part design:
- Reduce the thickness ratio
- This will minimize the race tracking effect of polymer melt
- Alter the mold design
Pay close attention to the proper placement of the vents,
- Place vents in the area that fill last.
- Vents are typically positioned discontinuity of mold material, such as at parting surface between the insert and mold wall, at ejector pin, and at mold slides.
- Redesign the gate and delivery system
- Changing the delivery system can alter the filling pattern in such a way that the last to areas are located at the proper venting location.
- Make sure the vent size is large enough so that the air present in the cavity can escape during injection.
Be careful, however, that the vent is not so large that is causes flash at the edge of mold. The recommended vent size is 0.025mm for crystalline polymers, and 0.038mm for amorphous polymer.
Adjust the molding condition:
- Reduce the injection speed.
High injection speed can lead to setting, which causes air to become entrapped in the part. Lowering the injection speed will give the air displaced by the melt sufficient time to escape from the vent.
Black specks/Black streaks:
Black specks and blacks streaks are dark spots or dark streaks found on the surface or throughout a molded part, brown streaks or specks refer to the same time of defects, except the burning discoloration is not as sever.
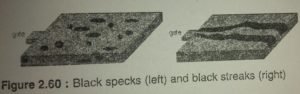
Causes of black specks/black streaks:
Black specks and black streaks are caused by over heated (degraded, burned) material or by contamination of the reason.
Material Degradation:
Overheated material can degrade and lead to black streaks. Material that stay in the nicked rough surface of the barrel wall and screw surfaces for a prolonged period of time after heating will char and degrade, resulting in the default/
Material Contamination:
Contaminate in the air or material, such as dirty regrind, forging material, different colour material, or blower melt temperature material, are vast most often lead to black steaks and black specks. Airborne dirt can also cause dark spot on the surface of a molded part. Other defect resulting from the same causes.
- Brittleness
- Burn marks
- Discoloration
Remedies:
- Handle the material carefully
Make sure know contaminated materials such as a dirty regrind are blended in to the original material. Put the cover on the hopper and all bins of material. Airborne that can contaminate the original material, leading to black spots.
Alter The mold design:
- Clean the ejectors and slides. The stickers cold by caused by the Greece or lubricants on the slides or ejectors.
- Improve the venting system. If the black specks are found at the end of flow paths or black spots, they are likely caused by a poor venting system. Compressed air trapped in cavity is sometimes ignited, leading to the defects.
- Clean and polish any nicked surface on the runner system to keep dirt from loading these area.
- Clean the mold before molding.
Select a proper machine:
- Size a proper injection machine for a specific mold. The typical shot size should be between 20-80% of machine injection capacity. Temperature sensitive materials, range should be narrowed down more. Plastic simultaneously softer can help you select the right size injection machine for a specific mold. This will he avoid resin remaining in the heated barrel for prolonged periods of time.
- Check for scratched or dented barrel screw surface that trap material. This cold lead to the material becoming overheated or burned.
- Check for local over heating by a run way heater band or a malfunction temperature controller.
Adjust the molding condition:
- Lower the barrel and nozzle temperature
Material degradation can result from a high melt temperature.
- Purge and clean the injection unit.
The black strecks might be caused by contamination from the barrel wall of the screw surface when molding with two materials, after switching from one material to the other, the mold material might not be purged from the barrel completely. This could generate defect during the molding the second material.
Avoid recycling rejected part with black specks and black streaks:
Recycling such part could lead to further contamination, unless they the used or part are in black or for which such defects are acceptable.
Brittleness:
A brittle molded part has a tendency to break or crack. Brittleness result from material degradation leading to shorter molecular chain length (thus lower molecular weigh). As a result, a physical integrity of the part is substantially less than the specification.

Causes of brittleness:
Brittleness is caused by material degradation due to the following:
- Improper drying condition
- Improper temperature setting
- Improper runner system and gate design
- Improper screw design
- Weld line weakness
Other defects resulting from the same causes are:
- Black specks and black strecks
- Burn marks
- Discoloration
Remedies:
Adjust the material preparation:
- Set proper drying condition before molding
Brittleness can be caused by excessive drying time or drying temperature such as at full heat for several day. Excessive drying either drives of volatiles in the plastic, making it more sensitive to processing, or degraded the material by reducing the molecular weight. Material suppliers can provide optimum drying condition for the specific material.
- Reduce regrind material. The brittleness could be caused by too much regrind material added in to the original virgin material.
- Change to high strength material since low strength material tend to become more brittle if process improperly.
Alter the mold design:
- In large the sprue, runner, end or gate.
Restrictive sprue, runner, gate or even part designing could cause excessive shear heating aggravates. An already overheated material, causing material degradation.
- Select a proper machine components
- Get a better sprue design for the material you are using to achieve a better mixed machine temperature.
- Contact material suppliers to get the right sprue design information to avoid improper melt mix or over heating that leads to material degradation.
Adjust Molding Condition:
- Reduce the barrel temperature and nozzle temperature
If the barrel and nozzle temperature are too high, the material in the barrel will be over heated leading thermal degradation and the colour change.
- Reduce the back pressure, screw rotation speed, or injection speed. Since shear heating can result in material degradation.
- With in the limit not to overheat the material, increase melt temperature, mold temperature or injection pressure if the weld line has a tendency to crack. See weld line and melt lineresult in material degradation.
Great article of the molding process faults. Was looking for this for a project. Will do injection molding with a small machine just to experiment. Thanks!
thanks for visiting this site. of course we will try to do our best.
Can you please provide PET precorm injection moulding faults, causes & remedies
Thank you for your valuable comments. surely we will try to update your subject soon.
sir very much informative article thanks lot for sharing this information sir we are in business of plastic recycling trying to establish finding difficult to get in profit finding difficulties in quality of granules.. thanks your article will help us
Amezia vision environment pvt ltd satara maharashtra
PH 8263896695
VERY INFORMATIVE ARTICLES