PROCESS CONTROL-PROCESS PARAMETERS IN INJECTION MOLDING
The injection molding cycle can be broken down in to 04 phase i.e Fill, Pack, Hold & Cooling/Plastication. The process begins with the mixing and melting of resin pellets. Molten polymer moves through the barrel of the machine and forced in to a steel mold. As the plastic fills and pack the mold, part take shape and begin to cool. The molded part is then ejected from the mold ready for finishing steps and assembly. While machine selection, material properties and part design all affect the out come of injection molding, five processing variable specific to injection molding can have as much or more impact on the success of this process. These variables are
Injection Speed
Plastic Temperature
Plastic Pressure
Cooling temperature and time
Control of these variables during each of the four phase of the injection molding process can help improve part quality, reduce part variation or increase overall productivity.
Phase 1: Fill:
The screw advance and plastic flow in to the mold. Flow characteristics are determined by melt temperature, pressure and shear rate. Injection speed the rate at which the RAM (screw) move is the most critical variable during fill. A polymer flow more easily as injection speed is increased. However injection speed that is too high can create excessive shear and result in problems such as splay and getting. More importantly, heat from a higher shear rate can degrade the plastic, which adversely effects the properties of the molded part.
The way in which plastics flow during fill is also affected by their viscosity, or resistance to flow polymers with high viscosity are thick and taffy like those with low viscosity are thinner and flow more easily. Melt temperature affects viscosity and to achieve the vest result should be maintained with in the temperature range recommended by the supplier.
Plastic pressure, another variable, increasing sharply during fill. The molten plastic can, in fact be under much greater pressure then is indicated by hydraulic pressure. It is important to understand the flow characteristic during fill of the material being used and to operate the process consistently.
Phase 2 Pack:
Is when the plastic melt is compressed and more material is added to compensating for any shrinkage during cooling. Approximately 95% of the total resin is added during fill, with the reminding 5% added during the pack phase.
Plastic pressure is the primary variable of concern during the pack phase. The screw maintained pressure in the melt, compensating for shrinkage, which can cause sinks and voids. Variation is the cavity pressures are a primary cause of deviations in plastic part.
It is important to completely fill the mold: avoiding over packing or under packing; since packing pressure determine parts weight and part dimensions. Over packing can cause dimensional problems and difficulty in injecting the part, while under packing can resolve in short shot, sink, part weight variation and warpage.
Phase 3 Hold:
Is affected by all five of the process variables describe earlier injection speed, plastic temperature, plastic pressure and cooling temperature and time. After the mold is packed the plastic is held in the mould until it is partially solidified and the gate freezes. The drop in plastic pressure reflexes the amount of shrinkage that occurs from cooling. One way to optimize this phase is to decrease the hold time until the part weight change. At that point the gate is no longer sealed and resin back flows out of the mould. If hold continue after the gate seal, cycle time increase, using more time and energy to produce the part. The key is to maintain pressure on the plastic until the gate freezes.
Phase 4 Cooling & Plastication:
Is generally the longest part of the molding cycle up to 80% of the cycle time. Optimize cooling time can yield substantial gains in productivity. Because the gates are sealed during this phase, cooling temperature and time are the only variables at work. The key to optimizing the cooling phase is to balance the desire to cool quickly against the amount of molded in stress the final part can with stand.
Cycle Time:
Typical process cycle time various from several second to tense of second, depending on the part weight, part thickness, material properties, machine setting specified to a given process.
The injection molding cycle can be divided in to several stages.
They are mold closing, filling, packing, cooling, molding opening and injection as shown here.
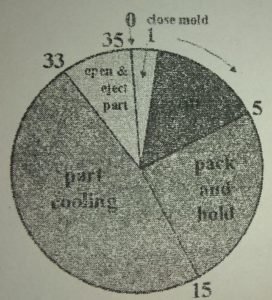
Cooling time is a major fraction of the total cycle time.
Cooling time is a function of:
- Mold wall temperature
- Melt temperature
- Material properties
- Part wall thickness
Wonderful work! This is the type of info that are supposed to be shared across the internet. Disgrace on the search engines for no longer positioning this submit upper! Come on over and discuss with my website . Thank you =)
thank you for your appreciation.